Aktuality
Historie závodu
Isover je nejvýznamnějším výrobcem izolačních materiálů, jednička na českém trhu. V celosvětovém měřítku Isover vyvíjí, vyrábí a prodává izolační materiály z minerálních vláken, čedičových i skleněných, již od roku 1936. Každá druhá střecha v Evropě je izolovaná materiály Isover, v USA každý pátý dům.
Isover je největší světový výrobce izolací s působností a výrobními závody po celém světě. Od eternitu přes Orsil až k Isoveru aneb výroba stavebních materiálů v Častolovicích.
Arnošt Bartoň založil v Častolovicích malou továrnu
V roce 1899 založil v Častolovicích malou továrnu na výrobu dehtových výrobků podnikatel Arnošt Bartoň.
Vynález původního eternitu
Vynález původního eternitu si nechal v roce 1900 patentovat Ludwig Hatchek, rodák z Těšetic u Olomouce. Eternit je nehořlavá látka s nízkou hmotností, složená z cementu a vláknitého pojiva, nejčastěji azbestu. Během II. světové války byl azbest považován za strategickou surovinu, výrobky z eternitu se tak vyráběly pouze v omezeném množství nebo byla jejich výroba zcela zastavena. Náhražkou azbestu se tak stala kamenouhelná dehtová smola a dřevocement. V minulosti byl eternit v podstatě synonymem pro střešní krytinu - má dlouhou životnost a výbornou funkčnost.
Chemická továrna dehtových výrobků
Kolem roku 1907 pak přebrali podnik dva společníci, August Kümmer a Karel Zöllner, a založili Chemickou továrnu dehtových výrobků Kümmer a Zöllner, společnost s ručením omezeným.
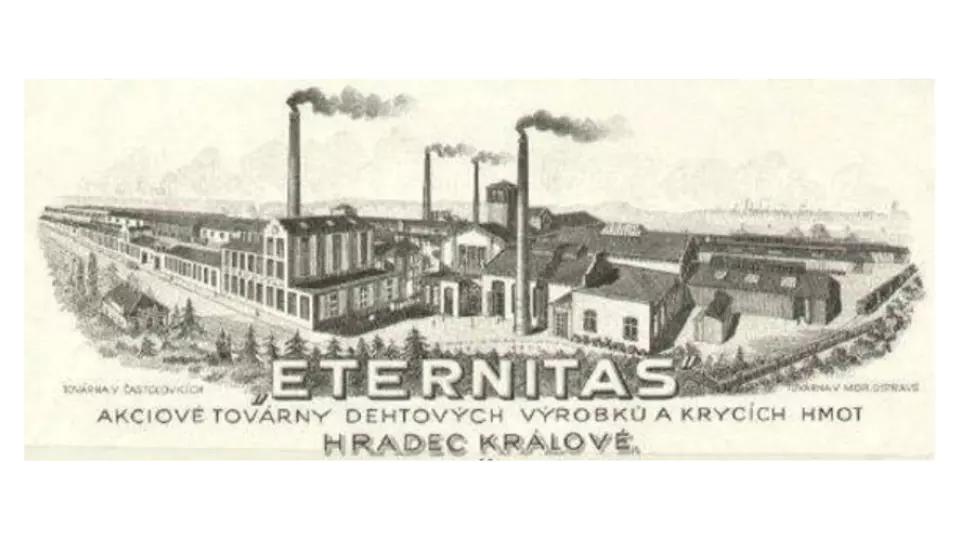
Vlastnictví společnost ETERNITAS
V roce 1921 přešel podnik do vlastnictví společnost ETERNITAS, akciová továrna dehtových výrobků a krycích hmot v Hradci Králové. Výroba dehtových výrobků a střešních krytin byla rozšířena také o břidlici, dále se v této společnosti rafinoval dehet, pryskyřice, vyráběl asfalt a asfaltová lepenka, izolační desky a dehtové oleje, umělé krytiny, a současně také ETERNITAS prováděl i stavby včetně pokrývačských prací. V této době továrna zaměstnávala 558 dělníků. Firma byla velmi úspěšná, např. zavedla vyškolení pokrývačských mistrů zdarma, čímž došlo ke snížení počtu stížností a reklamací na stavební práce až o 90 %. Společnost se dále rozrůstala a koupila Továrnu na asbestolit, spol. s r.o. v Moravské Ostravě.
Znárodnění a začlenění do Eternitových závodů
V roce 1945 byla společnost znárodněna a začleněna do Eternitových závodů, n. p. Praha. Kromě závodu v Častolovicích a Ostravě, byly znárodněny i podniky společnosti Eternitwerke Hatschek & Comp. - tedy Eternitové závody Hatschek a spol. v Šumperku a Eternitové závody Wildmann, Hatschek a spol. v Olomouci a Berouně. Od roku 1951 pak byla častolovická továrna přičleněna k národnímu podniku Českomoravské eternitové závody v Šumperku. V rámci přidružené výroby se začaly v továrně od roku 1953 vyrábět cementové překlady. Od 1. 9. 1961 pak přesídlila přidružená výroba stavebních hmot (betonárna) ze zadní části závodu v Častolovicích do Rašovic.
Zrušení závodu Českomoravské eternitové závody
Dne 1. července 1965 došlo ke zrušení závodu Českomoravské eternitové závody a výroba eternitových krytin byla v rámci tehdejšího socialistického hospodářství změněna na minerální plstě. Vznikl nový závod Stavební izolace n. p. Praha – došlo k přestavbě výrobní linky a k úpravě vlečky z častolovického nádraží.
První linka
Během roku 1966 se podařilo zcela zprovoznit první linku na výrobu minerálních izolací, v továrně v této době začali pracovat kromě Čechů také Vietnamci a Poláci, kteří byli ubytováváni v podnikové ubytovně. Roku 1978 byla postavena nová výrobní hala a instalována linka na výrobu lamelových skružovatelných pásů. Výroba izolací z minerálních vláken dále pokračovala, výrobní kapacita závodu byla v roce 1987 rozšířena instalací druhé linky ČA II a byla zahájena výroba tzv. orlických silikátů (orsilu).
Privatizace státního podniku Orsil Častolovice
V roce 1993 došlo k privatizaci státního podniku Orsil Častolovice někdejšími představiteli managementu. V roce 1994 přibyla nová linka ČAIII.
Vstup do koncernu Saint-Gobain
V roce 1996 vstoupil do Orsilu zahraniční kapitál koncernu Saint-Gobain a postupně došlo k rekonstrukci výrobních linek ČA I a ČAII.
Nový název společnosti Saint-Gobain Orsil s.r.o.
V následujícím období byl postaven sklad izolačních materiálů, zbourána a přemístěna administrativní budova i jídelna, a závod byl celkově rozšířen. Od roku 2000 se pak používal nový název společnosti, a to Saint-Gobain Orsil s.r.o.
Zvýšení výrobní kapacity
S rozšiřováním závodu se zvýšila i výrobní kapacita, v roce 2002 byla nainstalována první linka na výrobu produktů pro pěstování rostlin Cultilene.
Nový název Saint-Gobain Isover CZ, spol. s.r.o.
V roce 2009 společnost změnila název na Saint-Gobain Isover CZ, spol. s r.o. Následně v roce 2010 převzala výrobu polystyrenu s výrobními závody v Lipníku nad Bečvou a v Českém Brodě.
Součást akciové společnosti Saint-Gobain Construction Products CZ a.s.
Od roku 2012 je pak značka Isover součástí akciové společnosti Saint-Gobain Construction Products CZ a.s.
Isover součástí Saint-Gobain
Značka Isover patří do skupiny Saint-Gobain, jedné z nejstarších a nejprestižnějších ve Francii. Skupiny, která je zastoupena v 64 státech světa a zaměstnává 190 000 lidí. Skupiny, jejíž historie se píše už 350 let - první zakázka byla realizována v roce 1665 a jednalo se o 357 zrcadel do zrcadlového sálu ve francouzském zámku Versailles. Ale to už je zase jiná historie…
50. výročí
Závod Častolovice dne 2. 6. 2016 oficiálně oslavil své 50. výročí výroby minerálních izolací.
Proces výroby kamenné vlny
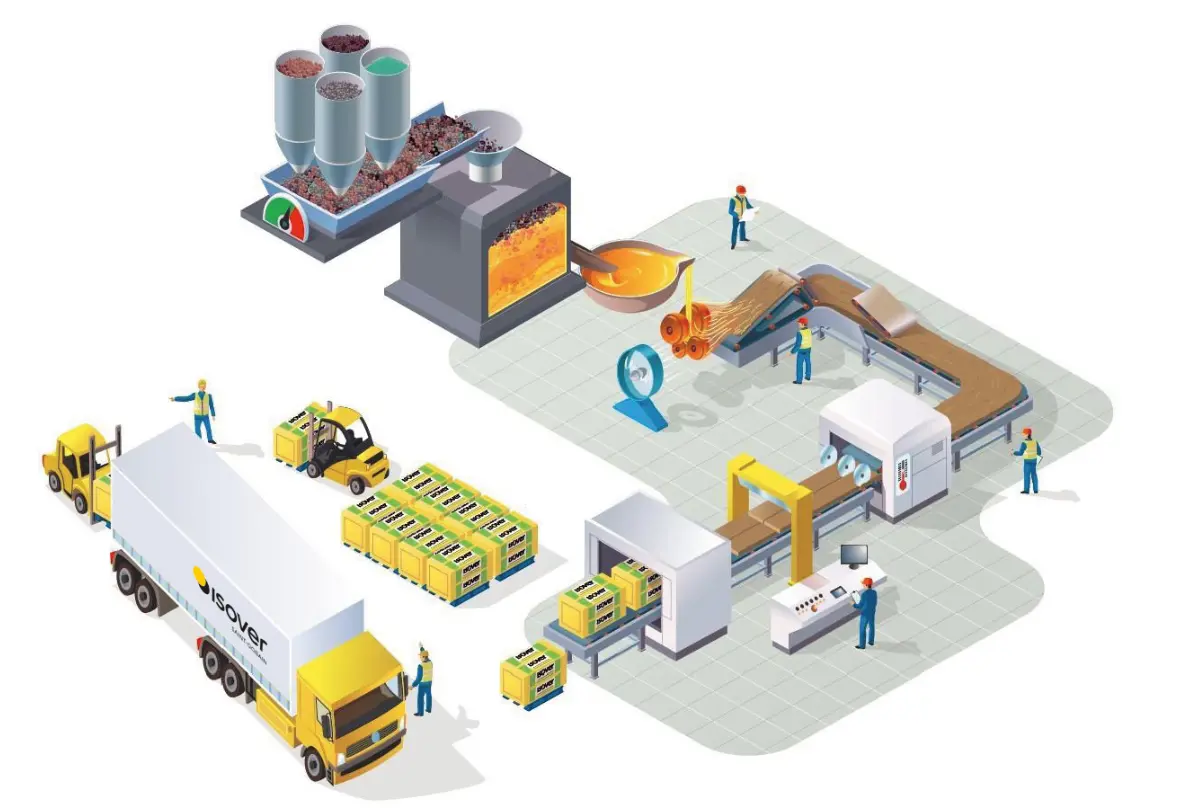
1 ŠARŽE
Čedič, struska a briketa (recyklovaná kamenná vlna) se skladují v silech, zváží se a smísí s koksem, čímž se vytvoří směs, která se umístí do kopule.
2 TAVENÍ
Směs se roztaví spalováním koksu v kopuli, která je vyhřátá na teplotu přesahující 1 500 °C.
3 ZVLÁKŇOVÁNÍ / STŘÍKÁNÍ POJIVA
Vlákna se tvoří stříkáním roztaveného skla na rychle se otáčející rotory. Na vlákna, která po pásu ve sběrné komoře pohání silný proud vzduchu, se automaticky rozpráší pojivo. Shromážděná vlákna tvoří primární homogenní rohož s nízkou gramovou hmotností. Tato rohož se přemístí na kyvadlové zařízení.
4 SKLÁDÁNÍ A STLAČOVÁNÍ
Kyvadlo skládá lehkou rohož do několika vrstev, čímž vytváří silnou vrstvu vláken. Tímto se upravuje její finální gramová hmotnost. Vytvarovaná rohož projde stlačovacím strojem, který svisle rovná její vlákna, čímž získává své mechanické vlastnosti.
5 VYTVRZOVÁNÍ / POLYMERIZACE
Pojivem naimpregnovaná rohož se přesouvá do vytvrzovací pece, která je zahřátá na více než 200 °C. Aby se pojivo polymerovalo, horký vzduch prochází rohoží z kamenné vlny. Toto rohoži dává její konečnou tloušťku, hustotu a konzistenci.
6 BALENÍ / PALETIZACE
Po vyjmutí z pece oříznou pily rohož tak, aby odpovídala požadované šířce. Odpad v podobě odříznutých okrajů se během výrobního procesu recykluje. Rohož z kamenné vlny se přesouvá k povrchové úpravě. Lze ji pokrýt papírem nebo hliníkem, skleněnou či asfaltovou vrstvou. Na konci linky se nachází válcovací stroj pro role a stohovací stroj a balič pro desky. Produkty se poté skládají na palety, což usnadňuje manipulaci, skladování a nakládání na přepravní jednotky.